How to leverage Lean and Six Sigma Process Improvement methodologies in Your Lawn Care Business
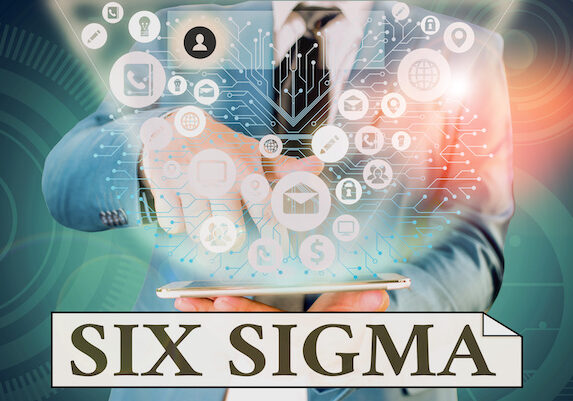
Anyone running a busy lawn care maintenance business should be looking to improve efficiency, cut costs, and increase profitability. As a result, from sales to service and invoicing, many lawn care companies are implementing Lean principles and Six Sigma methodologies into their daily operation.
If the term “Lean Six Sigma” is a new concept to you, let’s uncover how they relate to lawn care, landscaping, or tree care project management and business optimization.
In this blog post, we’ll explain what lean and six sigma are and how these small improvements can help your organization remove waste and overcome your biggest challenge.
What are Lean Six Sigma Principles?
Lean principles, also known as lean thinking, are commonly associated with a manufacturing process but it’s based on the idea of eliminating waste from any production environment. This means identifying and removing any steps or activities that don’t add value to the final product. By doing this, companies can streamline operations, reduce costs, and improve quality.
Some examples of waste when reviewing overall your job and project management efficiencies at your lawn care business can include:
Transportation costs – Has your lawn care business identified the most efficient and least expensive ways to transport lawn care supplies to your customer locations?
Wasted cycle time – Does your lawn care business track time spent on activities such as creating job proposals and invoices, as well as the time spent on the various jobs at a customer’s location?
Over-processing – Does your lawn care business do extra or unneeded work to add a feature that may not add value to the bottom-line?
Making mistakes – Does your lawn care business have a process for responding to errors/complaints so that the problem is fixed to everyone’s satisfaction?
What are Six Sigma Principles?
Six Sigma is a process improvement methodology that focuses on reducing defects and minimizing variability on a process. It uses data and statistical analysis to identify areas for improvement and to monitor progress.
The term Six Sigma stands for the standard deviations between minimum and maximum acceptable limits of quality that a customer expects. It was designed in the 1980s as a standard to measure productivity with regard to reducing defects in the manufacturing industry.
Although your lawn care business would not be considered a “manufacturer,” you share some common goals. With Sigma projects, and focusing on growth and continuous improvement, you can increase profitability. Day-to-day processes that flow smoothly means you can concentrate on the value that you bring to your customers.
Some core Six Sigma principles are:
- Streamline processes
- Reduce waste
- Concentrate on value
- Eliminate defects by removing variation
- Collaborate with your team to secure buy-in
As the one-stop-shop resource trusted by lawn, tree, and landscape companies, Arborgold offers some suggestions to introduce Lean/Six Sigma principles into your business operations.
Analyze Your Current Processes
First, identify all the steps involved in your lawn care operations to identify the facts and figures before looking for areas where you could eliminate waste or improve efficiency. Task your employees with these important questions, “Are there any steps that can be combined or completely eliminated? Is there any unnecessary movement or handling of equipment?”
Try Value-Stream Mapping
For all of your key processes, create a detailed workflow that maps out the steps that add value and those that don’t contribute to the bottom-line. You can develop a flowchart called a value stream and you can find examples of value map streams online to adapt for your organization. Use these maps as visuals to pinpoint areas of duplication or wasted time/effort.
Involve Your Team
The success of any long-term process initiative relies on the involvement and buy-in of your employees. Tell them about Lean/Six Sigma and why those principles are important to the success of your business. Involve them in the analysis process and value stream mapping. Challenge them to identify areas for continuous improvement and encourage them to suggest solutions to achieve the goals that the team sets collaboratively. Communicate often and with enthusiasm about the processes that are being analyzed and share the ongoing assessments with team members. When training is needed, don’t delay in providing it. If a team member comes up with a solution that translates into big cost or time savings, let everyone know how much you appreciate their willingness to eliminate waste and improve process flow.
Set Measurable Goals
Once you have established the areas for process improvement, set goals and metrics to measure progress. For example, you could set a goal to reduce the time it takes to complete a specific lawn care job by 10% within the next six months. Use data and statistical analysis to track progress and adjust as needed.
Implement Changes
Make it a point to move forward with the changes that you’ve identified. Monitor their impact on the time that your team spends on the jobs and on administrative tasks. You might need to adjust the way you estimate bids, schedule jobs, organize your equipment, or train your crews on any new processes. Ensure that everyone is aware of the changes and that they understand how to implement them without wasting time.
You may want to focus on implementing a “Just-in-Time” (JIT) system of inventory management of supplies such as seed, feed, gas, etc. JIT is another facet of Lean/Six Sigma thinking. As many manufacturers experienced first-hand, a JIT system helped to reduce inventory, labor costs and space, while increasing production and quality, among other benefits.
Continuously Improve
As mentioned above, Lean/Six Sigma principles are designed to be continuous improvement methodologies for all types and sizes of businesses – including yours! When you reach stated goals, revisit your value stream maps and continue to analyze processes, set new goals/objectives and monitor the metrics so your business can continue to reduce waste and increase profitability.
Ensure Customer Satisfaction
You’ve been reading many reasons why Lean/Six Sigma thinking and principles will take your lawn care business to the next level of success. Along with achieving better overall efficiency and a reduction in costs, another huge benefit is customer satisfaction. They’ll be so impressed with your company’s error-free professionalism and that can lead to four-star reviews online and a boost in word-of-month referrals.
“Lean” into Arborgold
Arborgold’s comprehensive software helps companies save time and money by coordinating jobs based on location and distance. We offer platforms for project management, supply chain management, time tracking with GPS, scheduling, and job management…you name it and we’ve got what you need to implement and sustain Lean/Six Sigma principles and practices.
Schedule an online tour of Arborgold today or speak to our product experts here.
Share this resource