Chemical Inventory Prep Made Simple for Plant Health Care Companies
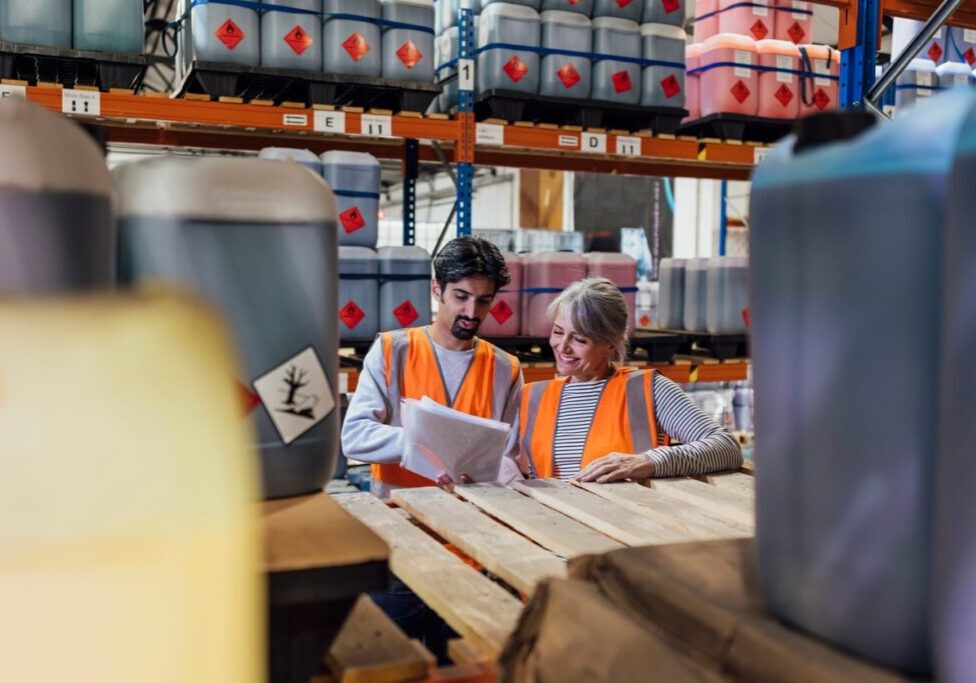
The busy season is fast approaching, and plant health care companies everywhere are gearing up for the annual chemical purchasing frenzy.
The big question: how much to buy? Buying in bulk can save significant money, but the risk of ending the season with a warehouse full of expired chemicals is a costly gamble. These are expensive products, and wasted dollars directly impact your bottom line. Effective chemical inventory preparation is crucial for plant health care companies to maximize profits, minimize waste, and ensure smooth operations throughout the year.
This article will provide you with the insights and strategies you need to master chemical inventory management.
The High Stakes of Plant Health Care Chemicals
For plant health care companies, chemical inventory management is more than just counting bottles. It’s a critical component of financial success. Whether you choose distributors like Rainbow Ecoscience or Arborjet for your chemical inventory needs, overbuying, improper storage, and expired chemicals directly inflate your Cost of Goods Sold (COGS), eating away at your profit margins.
Let’s say you purchase $10,000 worth of a specialized herbicide, but due to overstocking, $2,000 expires before it’s used. That $2,000 is pure profit loss. Add to that the expense of disposing of unused or expired hazardous waste, and the financial burden becomes even heavier.
Understanding chemical shelf life is paramount. Many chemicals have a limited lifespan, and careful planning is essential to avoid unnecessary waste. Proper storage, considering temperature, ventilation, and segregation of incompatible chemicals, presents further challenges. Overstocking only complicates these issues. Effective plant health care chemical inventory management is intrinsically linked to environmental health and safety.
Forecasting PHC and IPM Demand: The Key to Smart Buying
The key to avoiding overstocking is accurate demand forecasting. Integrated Pest Management (IPM) plays a crucial role here. Detailed treatment records from past seasons are invaluable. Analyzing this historical data allows you to identify trends, predict pest pressures, and estimate future chemical needs.
For example, when you’re tracking materials, if your records show a significant increase in aphid infestations last spring, you can anticipate a similar trend this year and plan your insecticide purchases accordingly. Don’t forget to consider external factors. Weather patterns, pest outbreaks, new environmental regulations, and even changes in client preferences can all influence demand. Proactively gathering such information helps you refine your forecasts.
Job Costing: The Foundation of Accurate PHC Estimates
Job costing is the cornerstone of accurate chemical inventory management. It involves tracking all expenses associated with a specific job, including labor, equipment, and, crucially, materials – especially chemicals. Why is this so important? Because accurate job costing enables you to determine precisely how much of each chemical is needed for a given task. This prevents both over- and under-purchasing.
Implementing effective job costing requires meticulous record-keeping. Track the quantity and type of chemicals used on each job, along with labor hours and other related expenses. This data becomes a goldmine of information for future estimates. By analyzing past job costs, you can refine your bidding process and ensure that your chemical orders align perfectly with your actual needs. This contributes directly to ensuring data accuracy in your inventory management system.
Technology to the Rescue
In today’s fast-paced world, technology offers indispensable tools for streamlining chemical inventory management. Software solutions like Arborgold, can significantly simplify inventory tracking, usage reporting, purchase order generation, and integration with job costing. These systems often provide inventory reports, enabling you to quickly assess your current stock levels and identify any potential shortages or surpluses. They also help with tracking materials and ensure data accuracy.
Learn more about the power of Arborgold Software for your plant health care business!
Practical Tips for Chemical Inventory Prep
- Conduct a Physical Inventory: Before placing any orders, start with a thorough physical inventory. Count every container, check expiration dates, and record the information in your chemical inventory system. This ensures data accuracy from the start.
- Organize Your Storage Area: A well-organized chemical storage area is essential for efficient inventory management. Clearly label all containers, group compatible chemicals together, and ensure easy access. This also helps with location-based inventory management.
- Implement a FIFO (First-In, First-Out) System: FIFO ensures that older chemicals are used before newer ones, minimizing the risk of expiration. This is a crucial aspect of chemical safety.
- Regularly Review and Update: Chemical inventory management is not a one-time task. Regularly review your inventory levels, track usage, and adjust your purchasing plans as needed. This helps you adapt to regulatory changes and maintain compliance with applicable laws.
Navigating the Regulatory Landscape: Hazardous Materials and Chemical Safety
Plant health care companies deal with various regulatory agencies and must comply with a complex web of environmental regulations concerning hazardous materials, toxic and hazardous materials, and hazardous waste.
Understanding chemical hazards, physical hazards, and health hazards is critical. Each chemical requires a Safety Data Sheet (SDS) (formerly Material Safety Data Sheet or MSDS) containing vital safety information, hazard information, hazard classifications, chemical exposure guidelines, and disposal instructions. Ensure you have the correct SDS for every chemical in your inventory, and that these SDSs are readily accessible to all employees. This is a critical component of effective hazard communication and chemical safety.
Staying informed about regulatory changes and ensuring compliance with all applicable laws is essential. This includes proper handling, storage, and disposal of hazardous chemicals. Understanding such information is crucial for protecting your employees, the environment, and your business.
Emergency Preparedness and Chemical Inventory Information
Your chemical inventory system plays a vital role in emergency preparedness. First responders need access to accurate chemical inventory information in case of a spill, fire, or other incident. Your inventory system should clearly identify the location of stored chemicals, their associated hazards, and any necessary emergency equipment. This information is crucial for effective hazard communication and protecting both your employees and first responders.
Remember that non-compliance with environmental regulations can result in significant fines and legal repercussions. Many organizations face challenges with chemical management, but a proactive approach to chemical inventory prep can mitigate these risks.
Data Accuracy and Inventory Reports
Data accuracy is paramount in chemical inventory management. Inaccurate data can lead to overstocking, shortages, compliance issues, and safety risks. Implement robust data entry procedures and regularly audit your inventory data to ensure its accuracy. Utilize your chemical inventory system to generate inventory reports that provide a clear overview of your current stock levels, expiration dates, and other relevant information. These reports are essential for informed decision-making and regulatory reporting.
Ready to Optimize Your Chemical Inventory?
Chemical inventory prep made simple for plant health care companies involves a multi-faceted approach. Accurate forecasting, diligent job costing, and the strategic use of technology are all essential components.
By implementing the tips outlined above, you can streamline your workflows, minimize waste, improve profitability, and ensure regulatory compliance. Don’t wait until the last minute. Start preparing your chemical inventory today and set your plant health care business up for a successful season.
Remember, effective chemical inventory management is not just about counting chemicals; it’s about protecting your business, your employees, and the environment.
Share this resource